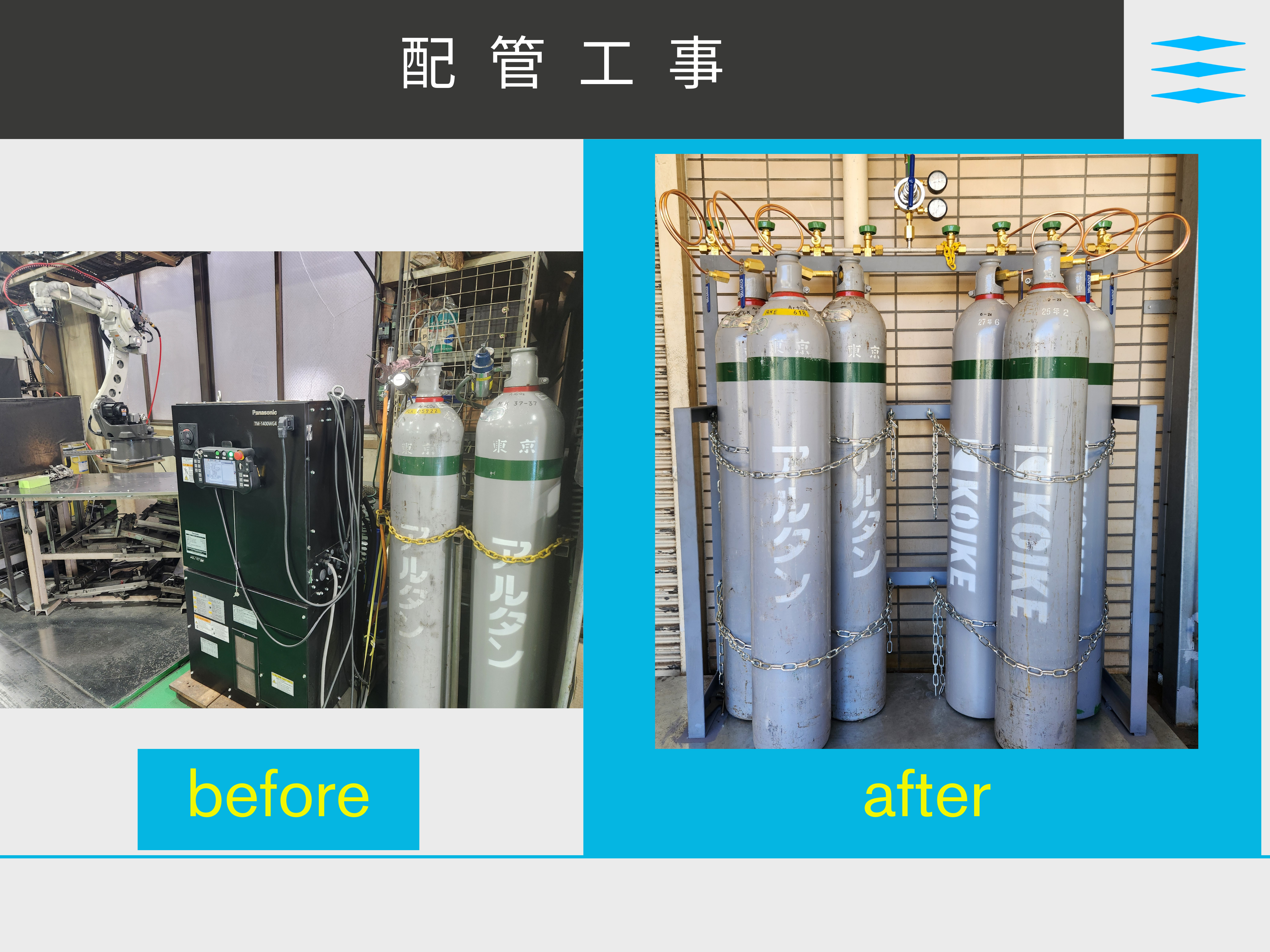
金属製販促什器の製造現場では、アルタンガスが必要不可欠です。当社工場では、各溶接機の供給ラインが独立していたことで作業効率や安全性に課題がありました。これらの課題を解決する為、供給配管の一本化を検討し改善を図ることにしました。
独立配管による作業効率の低下
各溶接機の供給ラインが独立していたことで溶接作業の流れが滞る要因となっていました。現場作業者は各配管のバルブ開閉を確認する等、各ラインの管理が煩雑であった為、作業効率を著しく低下させていました。異なるエリアで溶接作業を行う際、ガスの供給圧力が安定せず、作業スピードや品質にも影響を与えていました。
安全面のリスク
複数の供給ラインがあることは安全面でのリスクも増大していました。ガスの流れが複雑になることで、ガス漏れや圧力異常が発生した際の特定が困難になります。特に老朽化した配管が混在している場合には、継ぎ目や接続部からの漏れが発生しやすく、重大事故に繋がるリスクも高まります。単一の供給ラインであれば異常が発生した際に迅速に対応できますが、複数の供給ラインでは原因の特定に時間を要し、結果的に安全対策の遅れや長時間の稼働停止を余儀なくされます。
また、ガス缶の補充時には各所まで缶を転がして運搬していました。転がす際に缶が不安定になり、作業者の転倒や挟まれ事故を起こすリスクがありました。複数のエリアにガス缶を分散させることは、補充や管理の手間も増え、時間のロスが発生していました。
配管管理の煩雑さ
複数の供給ラインがあることでメンテナンスや定期点検の負担が増していました。各配管の耐用年数や定期点検のスケジュールが異なる為、管理者は各配管のメンテナンス計画を立てる必要があり、人的・時間的コストの面でも大きな課題となっていました。
一本化後の工場の変化
供給ラインの一本化後は、安定したガス供給により溶接作業を中断する頻度が減少しました。工場の作業効率が向上することで納期短縮に繋がった上、作業員の安全意識も向上し、事故リスクの低減も確認されました。更に、メンテナンスの負担が軽減さることで管理コストの削減にも繋がりました。
また、安全に供給できる仕組みを導入したことで運搬時の怪我のリスクも低減し、ガス缶の一括管理により在庫の把握が容易になり、無駄な補充作業も削減されました。小さな工夫が現場の安全性向上と業務効率化に大きく貢献しています。
まとめ
当社は、常に事業改善を追求し、より安全で効率的な製造環境を提供することを使命としています。技術革新と現場の声を活かし、持続可能な生産体制の構築を目指しています。これからも社会に貢献できる企業として、最新技術の導入や業務改善を進め、より良い製品を提供し続けてまいります。